La continuité numérique, clé d’une industrie décloisonnée

Pour améliorer le cycle de vie des produits, l’industrie automobile doit créer une continuité numérique, unifiant données et processus en temps réel. Dans son livre banc « Les 4 outils pour réussir dans la fabrication de véhicules zéro émission », Hexagon propose un système centralisé qui vise à éliminer les barrières entre partenaires, pour une fabrication plus fluide et agile, indispensable dans la transition vers des véhicules zéro émission.
Il est facile de dire que des outils tels que les simulations et les systèmes automatisés doivent communiquer entre eux, mais la mise en place de fils numériques pour les relier – et tout le reste – constitue un défi, car l’industrie automobile a tendance à être cloisonnée et fracturée. L’une des choses les plus difficiles dans le développement automobile est de fabriquer de nouveaux composants, parce qu’il faut réunir des équipes de différentes entreprises et situées à différents niveaux de la chaîne logistique. Le partage de données a toujours été complexe, car chaque pièce qui a été conçue est fabriquée dans une autre région et une autre entreprise.
Pour y remédier, le fabricant procédait de la manière suivante : une équipe réalisait une pièce, d’autres fabriquaient d’autres pièces, puis tout le monde itérait en fonction de ce que les autres avaient conçu. L’objectif du fil numérique est de briser ces silos afin que toutes les personnes impliquées dans le produit, de sa conception à sa fabrication et à sa maintenance, puissent travailler sur la base des mêmes données, en temps réel, à partir d’un référentiel unique. « Vous obtenez ainsi un produit qui peut être fabriqué dès la fin de la conception, sans aucune itération entre les organisations. Il est prêt à être réalisé », explique Stephen Graham, vice-président exécutif et directeur général de Nexus au sein de la division Manufacturing Intelligence d’Hexagon.
Décloisonner les données
Pour établir une continuité numérique, tous les outils et systèmes de stockage de données utilisés par l’entreprise et ses partenaires doivent communiquer en temps réel via le cloud. Cela complique encore plus la mise en œuvre, car l’interopérabilité et les verrouillages des fournisseurs limitent les systèmes pouvant communiquer. Il n’y a aucune garantie que deux divisions d’une même entreprise, encore moins des équipes de différentes entreprises, utilisent le même fournisseur de logiciels. Par conséquent, les véritables avantages des jumeaux numériques et des systèmes cloud n’ont pas encore été établis dans l’industrie. Mais Stephen Graham affirme : « Avec toutes les transitions observées dans l’industrie automobile à mesure qu’elle s’oriente vers des véhicules zéro émission, l’heure est venue de résoudre les problèmes de ces structures centralisées. Il est temps de décloisonner les données et de décentraliser pour permettre un travail plus flexible. »
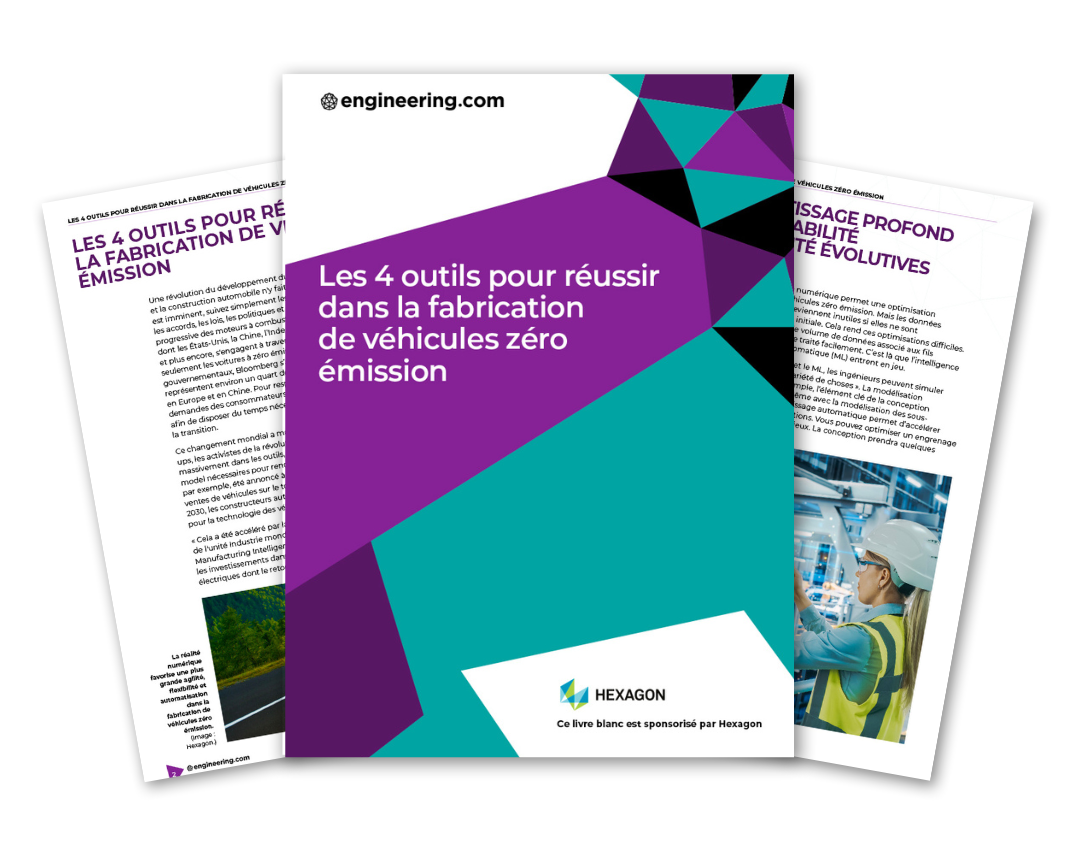
Téléchargez gratuitement le livre blanc « Les 4 outils pour réussir dans la fabrication de véhicules zéro émission ».
En accédant à un référentiel unique organisé et centralisé, les ingénieurs disposent ainsi de toutes les données dont ils ont besoin au moment opportun. Il n’est pas nécessaire de recréer une bride, parce que le fichier CAO approuvé est noyé dans un océan de données. Au lieu de cela, l’ingénieur recherche la bride et obtient en retour toutes les données et tous les fichiers dont il peut avoir besoin pour la pièce. L’équipe peut désormais faire en sorte d’achever la tâche le plus rapidement possible. Lorsque de nouvelles données arrivent sur la bride – par exemple, un autre ingénieur a modifié sa géométrie pour l’adapter à une charge plus importante, ce qui peut être le cas lorsqu’on passe des piles à combustible aux batteries – le premier ingénieur reçoit une notification et peut s’adapter rapidement aux changements. Ce scénario réduit considérablement les erreurs, les reprises et le gaspillage, tout en accélérant le délai de mise sur le marché. « Les ingénieurs veulent une solution qui leur permette de décloisonner les données entre les départements de conception, de production et de qualité, explique Kah Khoon Goh, vice-président des ventes et de la fabrication intelligente pour la zone ACI dans la division Manufacturing Intelligence d’Hexagon. Ils veulent une plateforme qui leur permette de collaborer efficacement avec les résultats issus de simulations, de fichiers CAO et de données de qualité. »
Naissance des jumeaux numériques de cycle de vie
Cette connectivité n’améliore pas seulement les conditions de travail des ingénieurs. Elle optimise aussi les outils et systèmes qu’ils créent. Par exemple, en veillant à ce qu’une simulation 1D ait accès aux données les plus récentes, les ingénieurs peuvent obtenir des informations en temps réel. « L’intégration des processus de fabrication avec les appareils de métrologie et la gestion numérique de la qualité pour collecter des données du monde réel, est de plus en plus importante, souligne Masaki Konno. Ces données peuvent ensuite être comparées à des simulations originales, ce qui génère une boucle de rétroaction d’amélioration continue. Bien qu’elles se situent encore à un stade précoce, diverses initiatives sont en cours pour améliorer l’intégration des processus de fabrication et de développement. »
En étendant cette logique au-delà de la fabrication et de la conception, il est facile de voir que les jumeaux numériques peuvent aider à simuler, surveiller et optimiser un cycle de vie complet dans l’optique de la durabilité. « En intégrant continuellement les retours d’information dans les processus de production et d’ingénierie, nous pouvons diminuer considérablement les défauts de fabrication », poursuit Takashi Isaji, directeur général du développement commercial pour le Japon dans la division Manufacturing Intelligence d’Hexagon. Et d’ajouter : « Nous pouvons également définir des alarmes pour des problèmes tels que les fixations de gabarit, l’alignement ou les changements d’outils afin d’exclure la production de produits de moindre qualité. La connectivité doit s’étendre à l’ensemble de l’usine pour permettre aux clients de surveiller leur équipement et de résoudre toute erreur ou tout dysfonctionnement en ligne, ce qui évite des visites sur site. »
- Tiré du livre blanc Hexagon « Les 4 outils pour réussir dans la fabrication de véhicules zéro émission »
- Prochain article : « L’IA et l’apprentissage profond rendent la durabilité et la productivité évolutives »
- À lire aussi : « Pourquoi le prototypage numérique va révolutionner le développement des véhicules zéro émission »
- A lire aussi : « Adaptation et automatisation : les clés de la transformation durable de l’industrie automobile »