Des alliages métalliques révolutionnent la production d’hydrogène
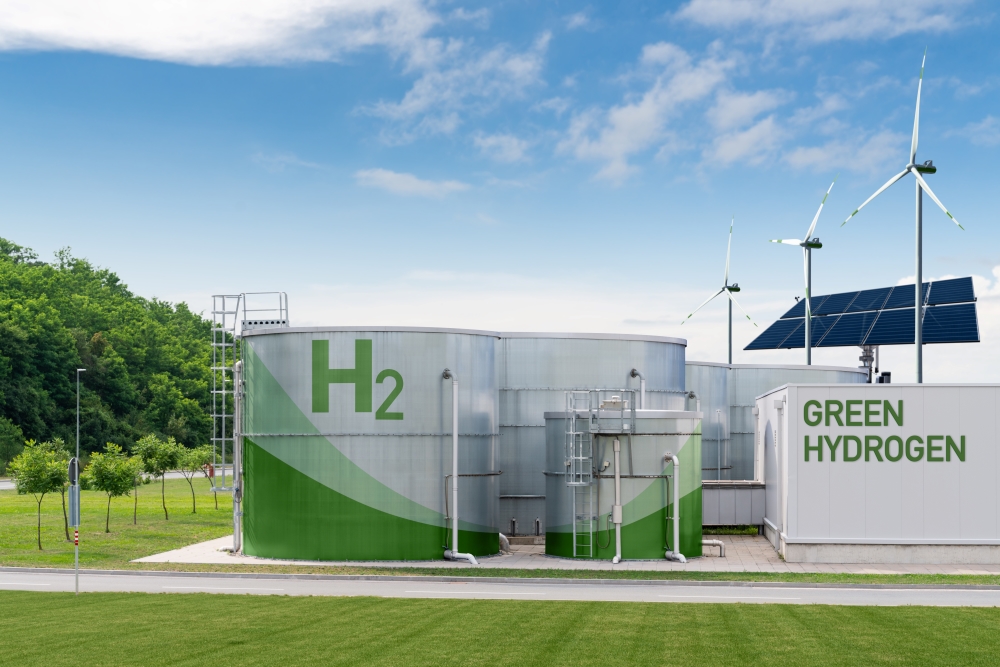
Des chercheurs grenoblois ont publié, dans la revue Nature Materials, leurs travaux démontrant qu’il serait possible de remplacer l’oxyde d’iridium, utilisé comme catalyseur dans les électrolyseurs alcalins, par des alliages fer-nickel-chrome, beaucoup moins coûteux, facilement disponibles et recyclables.
C’est dans la prestigieuse revue scientifique Nature Materials que deux chercheurs français, Valérie Parry et Marian Chatenet ont publié leurs travaux démontrant qu’il serait possible de remplacer l’oxyde d’iridium, utilisé comme catalyseur dans les électrolyseurs alcalins, par des alliages fer-nickel-chrome, beaucoup moins coûteux, facilement disponibles et recyclables.
En quoi cette révélation peut bouleverser l’activité des énergies renouvelables (ENR) ? Alors que cette source, éolienne et solaire principalement, est par nature intermittentes (éolien, solaire…), elle rend de plus en plus complexe la gestion des réseaux électriques. Alors que la production d’hydrogène par électrolyse de l’eau offre un moyen efficace d’utiliser l’électricité excédentaire issue des ENR. L’hydrogène produit peut ensuite être soit reconverti en électricité en période de forte demande, soit être injecté dans le réseau de gaz naturel et/ou utilisé comme réactif chimique (agent réducteur).
Métaux rares
Il faut savoir que l’électrolyse alcaline est la plus utilisée à l’échelle industrielle, par opposition à l’électrolyse en milieu acide qui nécessite d’utiliser des métaux rares comme le platine et l’oxyde d’iridium, fait-on savoir au sein de Grenoble INP, institut d’ingénierie et de management, qui a participé aux travaux des deux chercheurs. En plus d’être particulièrement coûteux, la disponibilité de ces matériaux est problématique. « A l’heure actuelle, on extrait 7-8 tonnes d’iridium par an, et les réserves connues sont de 800 tonnes (hypothétiquement 3 000 t), indique Marian Chatenet, chercheur au Lepmi, le laboratoire d’électrochimie et de physicochimie des matériaux et des interfaces dont la tutelle est l’INP grenoblois. Or, pour atteindre les objectifs fixés dans le cadre de France 2030, il faudrait attribuer environ 15 % de la production mondiale au pays, ce qui est irréalisable. Il faut donc trouver des alternatives. »
Il y a 15 ans, Marian Chatenet raconte s’être fortuitement aperçu que l’acier pouvait remplacer l’oxyde d’iridium pour catalyser l’électrolyse alcaline de l’eau (ou tout du moins la réaction de dégagement de l’oxygène, la plus difficile de l’électrolyse de l’eau). Fin 2019, il s’associe à Valérie Parry, chercheuse au SIMaP (Science et ingénierie des matériaux et procédés), structure issue de la fusion de trois unités de recherche du CNRS, de Grenoble INP et de l’UGA, afin de comprendre le lien entre les propriétés catalytiques et la composition de plusieurs alliages industriels à base de fer, de nickel et de chrome (inox, Incoloy, Inconel…). « Si l’activité catalytique de ces compositions n’est pas optimale au début, on s’aperçoit qu’au bout d’un temps plus ou moins long, une couche active d’oxydes se forme en surface, laquelle est très efficace pour dégager de l’oxygène en milieux alcalin », poursuit Marian Chatenet.
Couche d’oxyde
En outre, il apparait que la composition de la couche active finale dépend essentiellement des teneurs en fer et nickel de l’alliage de départ, rapportent les chercheurs. Par ailleurs, l’équipe du Lepmi a développé un protocole permettant d’accélérer le développement de la couche d’oxyde et sa stabilisation, en quelques heures seulement.
Toujours en collaboration avec Valérie Parry, les chercheurs ont également testé l’influence de la mise en forme de l’alliage (tréfilage ou laminage, par exemple) et son état de surface sur son activité catalytique. « Que ce soit en termes de coût de matière première ou de simplicité d’élaboration et de mise en forme du matériau, les alliages fer-nickel-chrome se révèlent bien plus avantageux que l’oxyde d’iridium », assure le chercheur du Lepmi. L’INP ajoute que l’industrialisation de la filière permettra, en plus de résoudre le problème de disponibilité des matériaux, de réduire le coût de l’électrolyseur de près d’un tiers. « Et en plus, ça se recycle facilement », note M. Chatenet.
Développement à grande échelle de l’électrolyse de l’eau
La preuve de concept étant faite, reste à réaliser toute l’ingénierie en aval. Dans le cadre du PEPR Hydrogène, le programme et équipements prioritaires de recherche de France 2030, le projet DAEMONHYC vise, lui, à développer des électrolyseurs à membranes anioniques sans métaux nobles, en optimisant le choix des matériaux et leur mise en forme. Objectif : permettre le développement à grande échelle de l’électrolyse de l’eau. Et les alliages fer-nickel-chrome sont à la base de ces recherches.
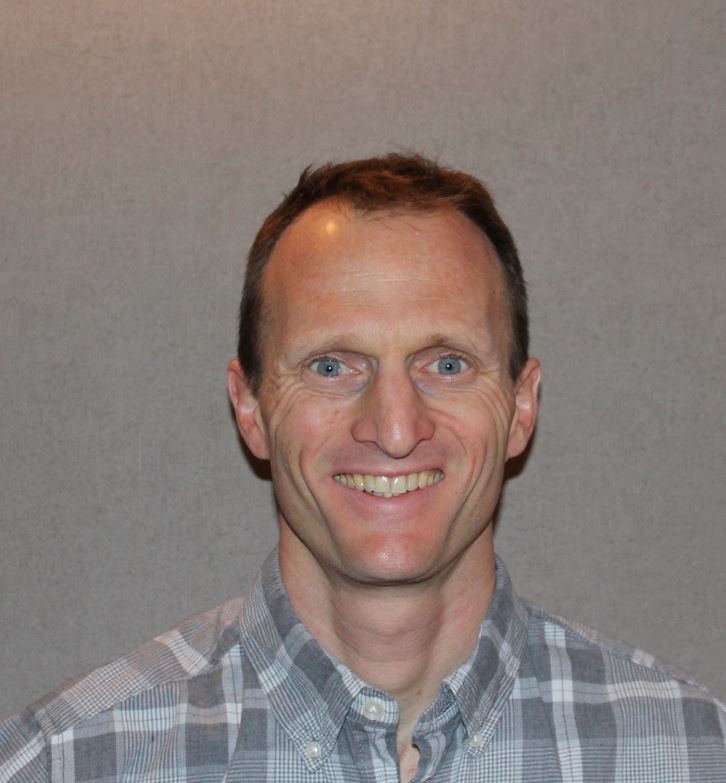
Marian Chatenet, chercheur au Lepmi, à Grenoble.
à propos de fabrication
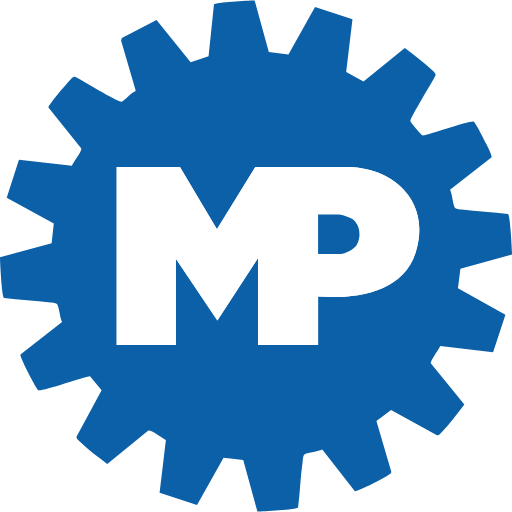