Une cellule robotisée pour la productivité
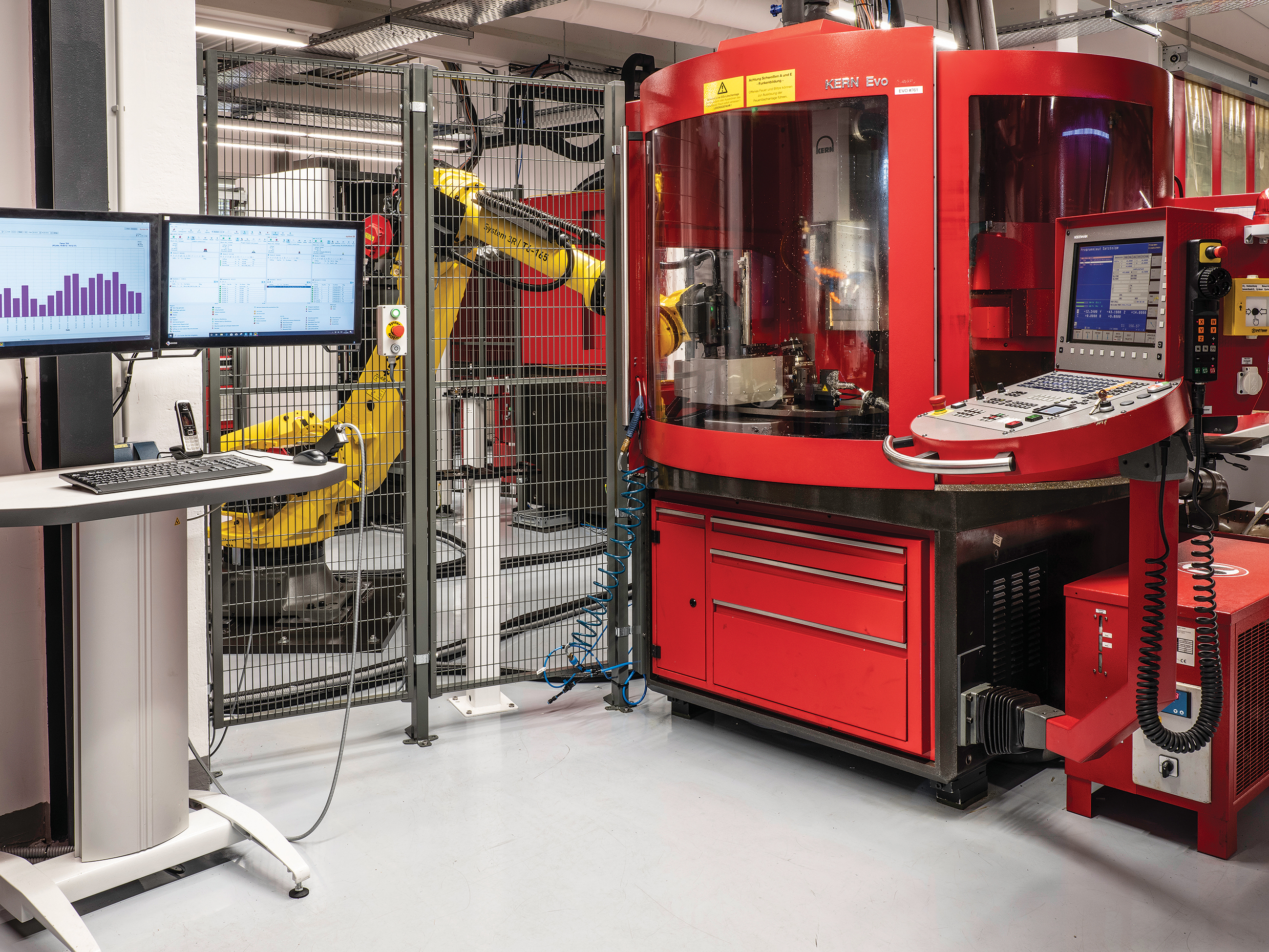
Un fabricant allemand, spécialisé dans les pièces extrêmement complexes et précises, propose pour augmenter encore la qualité et la productivité, des solutions d’automatisation innovantes. On peut citer en exemple une cellule robotisée avec quatre centres d’usinage.
La plus haute précision a toujours été une force de l’entreprise Kern Microtechnik en Haute-Bavière. Les machines fabriquées sont testées dans leurs propres ateliers. L’entreprise est à l’écoute de ses clients afin de fournir les meilleures solutions. Le marché, aujourd’hui, est confronté à du manque de personnels qualifiés. En discutant des stratégies futures, l’idée est venue d’augmenter l’automatisation et d’avoir un robot fonctionnant avec quatre machines. Patrick Ginzel, responsable de la gestion technologique, est devenu responsable de ce projet. Il explique : « Nous avons décidé de chercher de nouvelles idées et des sources externes intégrées pour trouver la meilleure solution pour notre automatisation. »
Automatiser pour mieux produire
La tâche du robot est de fabriquer des pièces exigeantes avec des précisions au micron et des surfaces de l’ordre du nanomètre et ceci 24 heures sur 24. Aucun personnel n’est nécessaire pour les quarts de nuit ou de week-end, l’alimentation des pièces s’effectue avec un système de palettes. Le contrôle complexe de la cellule de fabrication est effectué par le système de contrôle de processus WorkShopManager. Le robot est articulé avec une longueur d’extension de plus de trois mètres (9 pieds). « Étant donné que le robot doit travailler avec quatre centres de fabrication – deux Kern Micros et deux Kern Evos – l’extension est pertinente », explique M. Ginzel. Et d’ajouter : « De plus, deux magasins rotatifs sont utilisés avec 250 emplacements de palettes. C’est là que les palettes – marquées de puces RFID – et leurs pièces sont stockées, prêtes à l’emploi ! ».
Les quatre centres d’usinage sont toujours préparés pour différentes pièces. Cela signifie qu’un nombre correspondant de programmes CNC et leurs données de fabrication sont stockés dans le WSM, plusieurs jeux d’outils sont configurés et des ébauches sont stockées dans le magasin rotatif pour toutes les pièces. En conséquence, même un outil cassé ne ralentit pas le système. Si le pire du pire arrive, le PLS détecte le problème et passe immédiatement à la pièce suivante sur la machine concernée.
Cela devient important lorsque le personnel n’est pas là. Bien sûr, les machines reconnaissent également la défaillance de l’outil sans WorkShopManager. Cependant, ils arrêtent le processus jusqu’à ce que l’échec soit résolu, généralement par les opérateurs. Les heures de travail de ces quatre machines dépassent les 90 heures par jour avec cette stratégie numérique. En théorie, 96 heures sont possibles. Ainsi, avec 90 heures, le centre d’usinage a plus de 94 % de sa capacité utilisée.
Un autre avantage est, comme l’explique Sebatian Wühr, directeur de l’usine de sous-traitance Kern, qu’il a besoin de moins d’employés pour un fonctionnement fiable de cette cellule robotisée : « Habituellement, nous avons besoin d’un membre du personnel qualifié pour le fonctionnement de chacune de nos machines. Comme il est difficile pour le moment de trouver des personnes qualifiées, cette situation s’est améliorée grâce à cette cellule robotisée. » Patrick Ginzel confirme : « Il est facile de travailler avec le PLS et l’écran tactile. Un membre de l’équipe qualifié avec le soutien d’un ou deux membres de son équipe en formation peut facilement faire fonctionner la cellule. »
Une gestion des capacités
Le technicien qualifié est responsable des tâches complexes comme la mise en place de nouveaux produits en analysant la durée de vie des outils. Il élimine les dysfonctionnements, optimise le processus et organise les cycles. Ses collègues préparent les ébauches, changent les outils lorsque leur durée de vie – selon PLS – arrive à son terme, mesurent les pièces à l’aide d’un tableau de contrôle de la qualité et acheminent les pièces finies au poste de nettoyage.
Ce à quoi devaient s’attendre les deux ingénieurs Patrick Ginzel et Sebastian Wühr est devenu réalité. L’investissement dans une cellule de robot porte ses fruits. Les temps non productifs ont considérablement diminués et une augmentation à deux chiffres de la productivité en résulte. M. Ginzel explique : « Avec ces mesures, nous avons même dépassé notre objectif de 25 %. »
à propos de fabrication
les plus lus
à lire aussi
Les nouveaux produits

Lampes à LED pour machines dans boîtier en aluminium 5 600 K, à intensité variable, 24 V CC, verre de sécurité
Lampes à LED pour machines dans boîtier en aluminium 5 600 K, à intensité variable, 24 V CC, verre de sécurité